Intercompany planning
In some cases, companies have different legal entities for different business purposes. For example, for the car manufacturing business, we can have a legal entity that buys and sells car parts, another legal entity that manufactures and sells cars, and a third company that handles car repair services.
Extending our scenario, we can have segregated operations as follows:
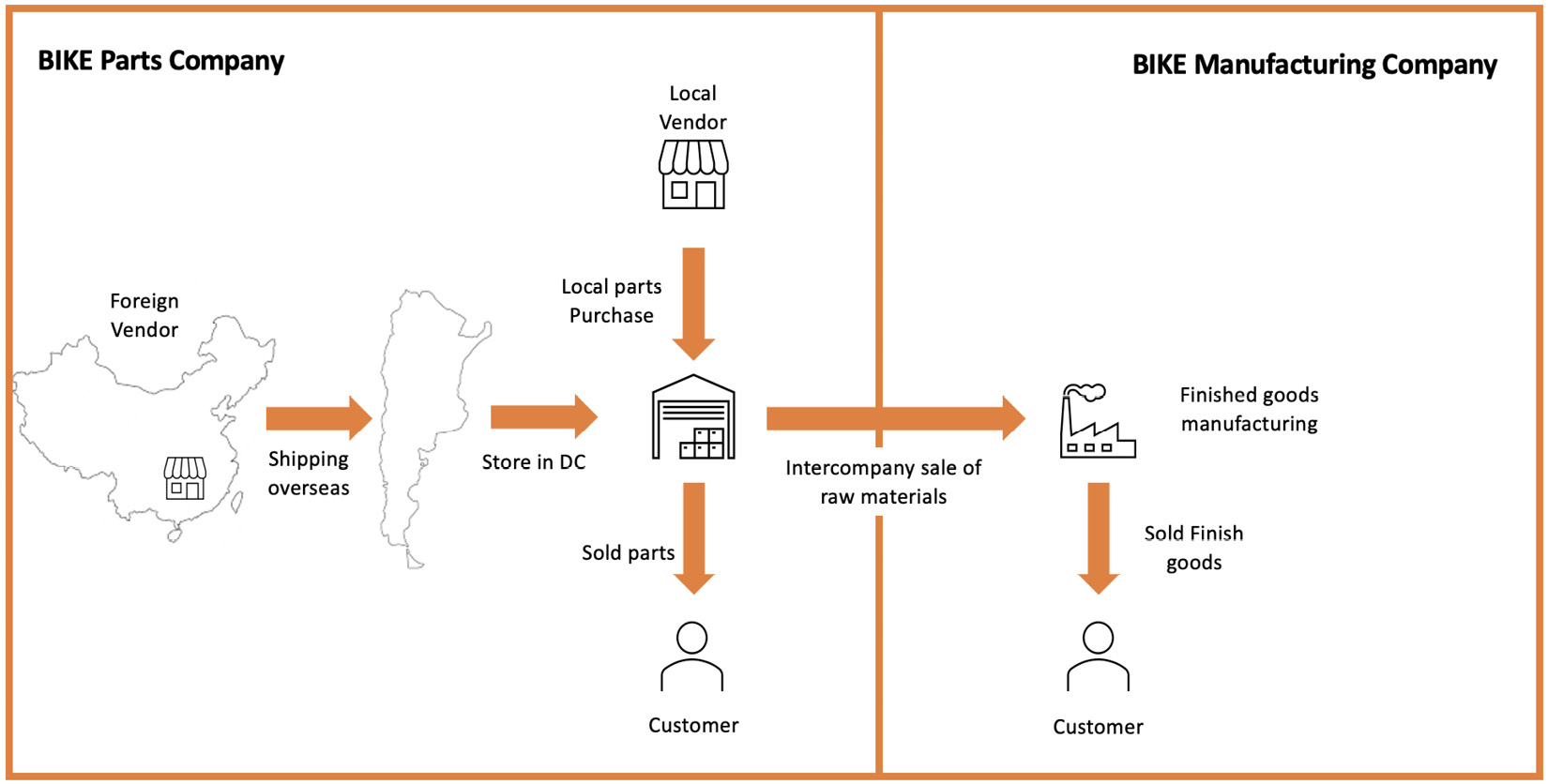
Figure 11.17 – Intercompany planning scenario
This scenario is the same as what was described in the previous section, but now, the manufacturing process is done by another legal entity of the same group, forcing intercompany planning.
From the bike manufacturing company, we will create or plan production orders, and that demand will be transferred to the bike parts company, which will plan their purchase accordingly.
We need to start by configuring the following:
- Intercompany planning groups
- Intercompany trade
- Demand forecasting/or...